14.07.2025
Achieve Longer Tool Life and Boost Productivity with MAS GND Parting and Grooving System
Manufacturing facilities can achieve up to 30 percent longer tool life in parting and grooving operations by utilizing the MAS GND parting and grooving system.
This system features square shanks available in 16 × 16, 20 × 20, and 25 × 25 mm cross-sections. These shanks are designed with internal coolant channels, ensuring that coolant-lubricant is delivered directly to the cutting edges of Sumitomo parting inserts. These inserts are available in widths ranging from 1.25 to 8 mm. The GND parting and grooving system allows for plunging depths of 12, 17, 22, or 32 mm.
Optionally, coolant-lubricant can be fed into the tool shanks from the side, rear, or bottom. This eliminates the need for external piping and hoses, thus removing undesirable interfering contours. The internal coolant channels effortlessly handle pressures up to 20 bar.
The coolant exit, located just a few millimeters above the rake face of the parting inserts, ensures the coolant reaches directly beneath the flowing chips. This reliably lifts the chips away. Even when grooving challenging materials, chips break short and are continuously evacuated from the cutting zone. Furthermore, the coolant jet consistently and reliably cools the parting edge.
Extensive Range of Variants
All insert variants from carbide manufacturer Sumitomo's product line are available as parting inserts. This specifically includes versions made from the AC1030U cutting material grade. This grade consists of particularly tough, fine-grained substrates with a multi-layered, extremely well-adhering PVD coating.
These inserts, featuring ground cutting edges and chip breakers, offer exceptional resistance to wear and cutting edge chipping. Additionally, the smooth coating prevents adhesion. This is particularly beneficial when machining difficult materials, such as 34CrMo4, C45, X6Cr17, and X5CrNiS18-10.
Doubled Tool Life
For instance, when grooving bars made of 15NiCrMo 16 5 stainless steel, GCMN 2002 parting inserts made from AC530U cutting material with GF chip breaker geometry achieve up to six times longer tool life.
These tools operate at a cutting speed of 180 m/min and a feed rate of 0.1 mm per revolution, plunging from a bar diameter of 30 mm to a depth of 11 mm. Up to the wear limit due to flank wear, the tools part off approximately 2000 components per cutting edge – more than double the tool life previously achieved with inserts from a competitor.
More Productive in Series Production
Key advantages of the GND parting and grooving holders in conjunction with Sumitomo parting inserts include high process reliability and significantly extended tool life. This leads to considerably longer intervals between tool changes and, consequently, less machine downtime.
As a result, manufacturing companies can operate more productively and efficiently, especially in series production, such as in the automotive industry and among its suppliers.
Fast, High-Precision Tool Changes
To specifically minimize tool change times on automatic lathes, the GND parting system is also available as a quick-change head for MAS's "PZturn" quick-change system. This allows GND parting tools to be changed in the working areas of automatic lathes in the shortest possible time, with approximately 5 µm change accuracy, without removing and re-installing holders.
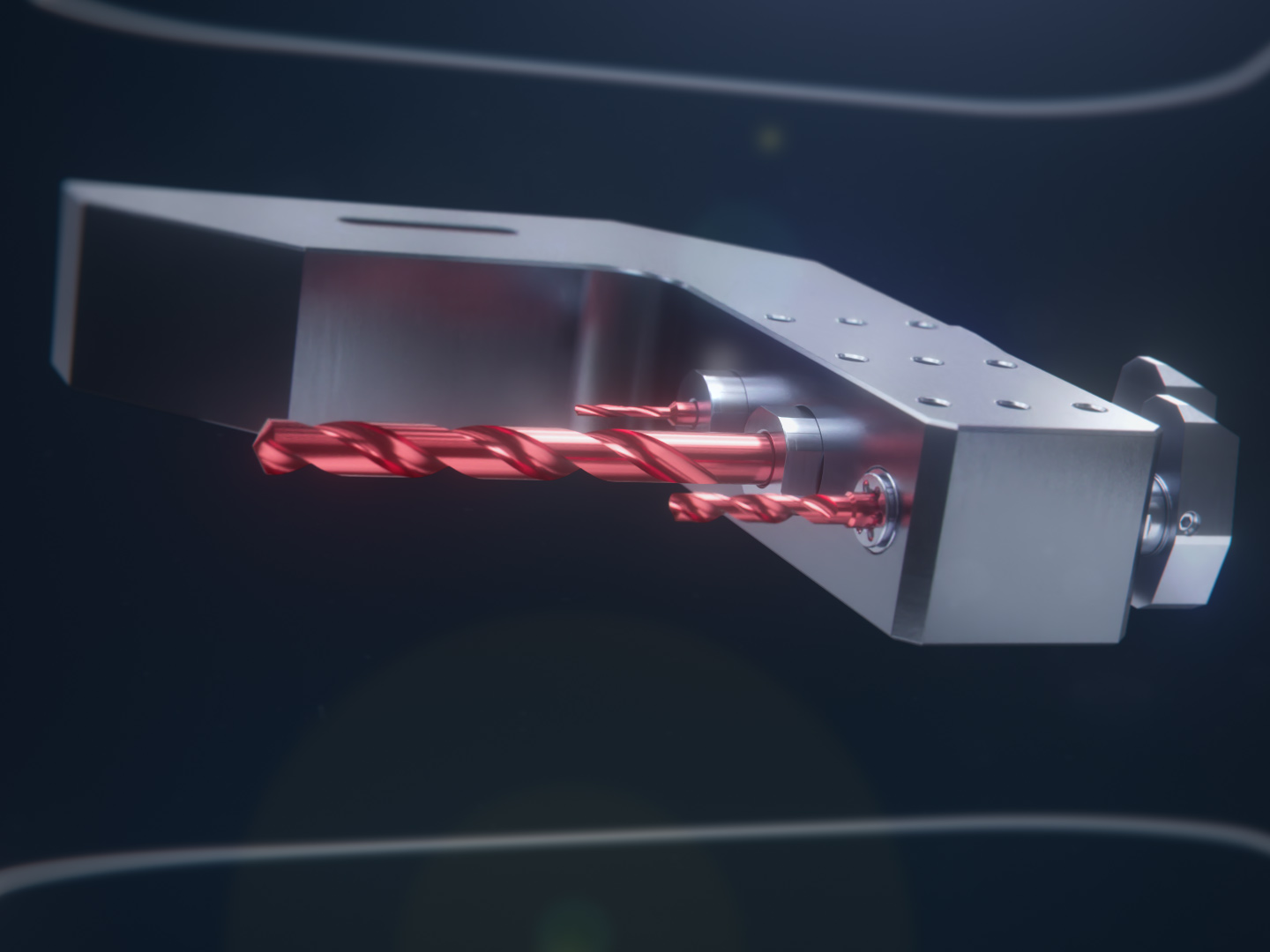